Introduction to Brushless Motor Solution
Note
This document is automatically translated using AI. Please excuse any detailed errors. The official English version is still in progress.
Overview and Advantages of BLDC Solution
Espressif’s Brushless Motor (BLDC) solution offers excellent performance and stability, and can be paired with ESP master chips that support MCPWM peripherals. This solution performs well in various application scenarios such as household appliances, industrial automation, power tools, and medical equipment. Advantages include rotor initial phase detection, sensorless speed control, etc. In addition, it supports back-EMF detection with hardware comparators and internal ADCs, enabling speed closed-loop control. Here is an overview and advantages of the BLDC solution:
Higher operating efficiency and performance: Utilizing the high-performance processing capability of the ESP chip, it can monitor and estimate the operating status of the brushless motor in real time, achieving stable closed-loop control.
Rich software and hardware references: Provides comprehensive BLDC software and hardware development materials, including detailed development documents and examples. In addition, related hardware design files are open source, making it easy for customers to quickly build prototypes.
Complete control scheme: Supports sensorless square wave control based on comparators or ADCs, and sensor-based FOC. Among them, the sensor-based FOC control scheme based on SimpleFOC supports IDF framework development, meeting the needs of different user groups.
In addition, Espressif also supports the following features to further expand the application scenarios of the BLDC solution:
RainMaker private cloud deployment: Integrated one-stop private cloud deployment, providing users with more convenient BLDC interaction methods and remote OTA upgrade services.
High-performance floating-point operation performance: Optimizes the trigonometric and floating-point operations of the SimpleFOC algorithm, improving the algorithm efficiency of BLDC.
Common Application Scenarios of BLDC
Espressif’s BLDC solution is widely used in various fields, including but not limited to:
DC frequency conversion floor fan solution: Integrated with Wi-Fi, BLE, RainMaker, supports speed adjustment, oscillation control, natural wind speed and other functions. Typical application scenarios are small household appliances.
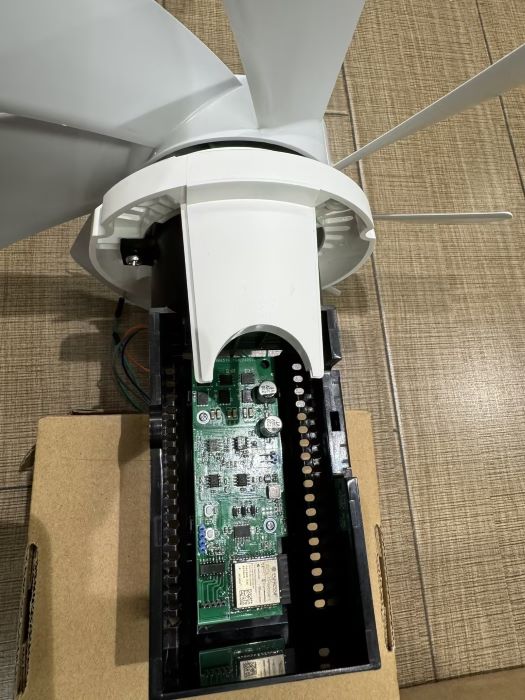
SimpleFOC single motor drive solution: Integrated with SimpleFOC algorithm, supports motor parameter verification, speed closed-loop, angle closed-loop and torque closed-loop. Typical application scenarios are small household appliances and industrial automation applications.
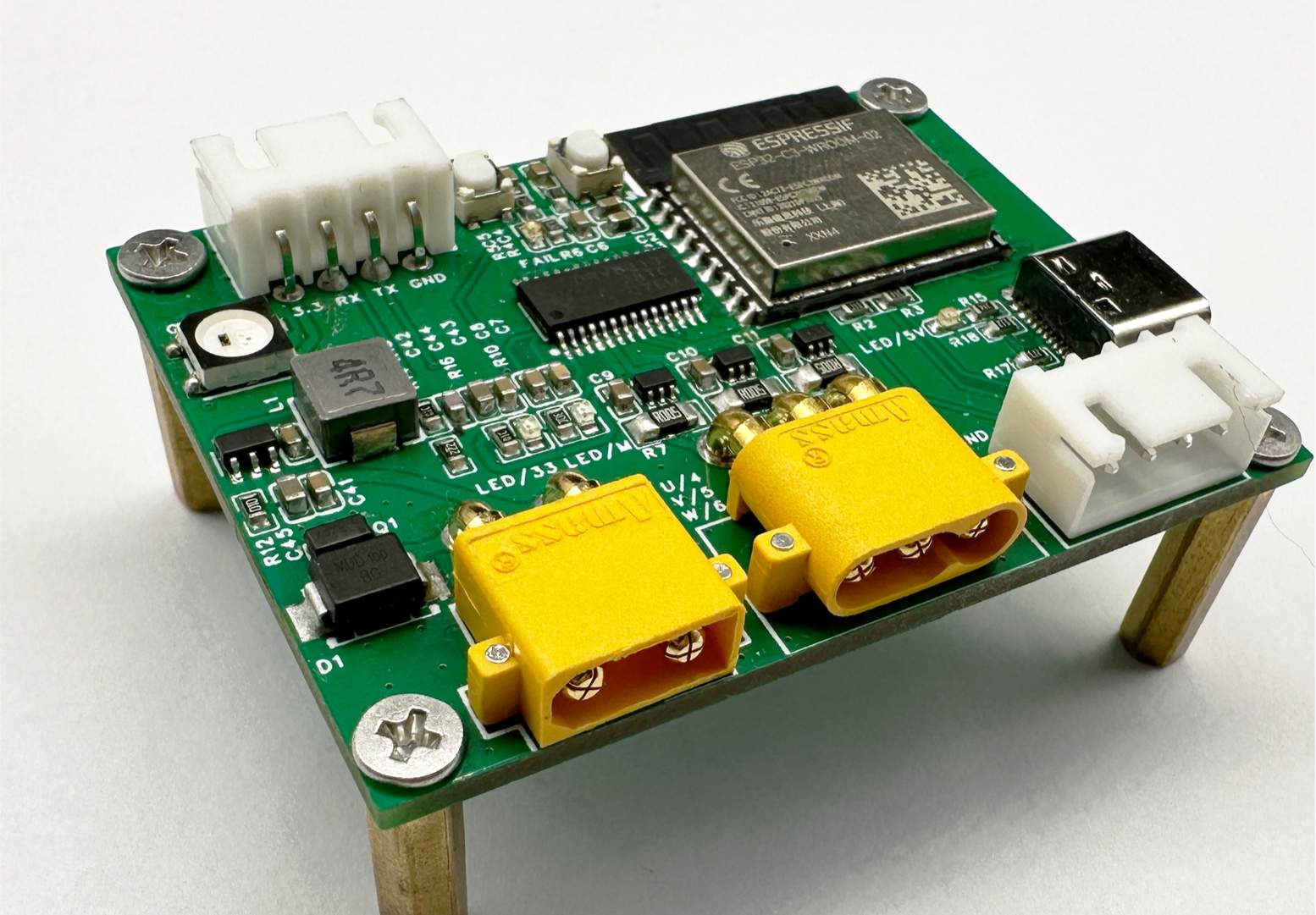
FOC knob screen solution: Integrated with SimpleFOC algorithm, supports knob screen display, ratchet hand feel simulation, etc. Typical application scenarios are knob screen applications in small household appliances.
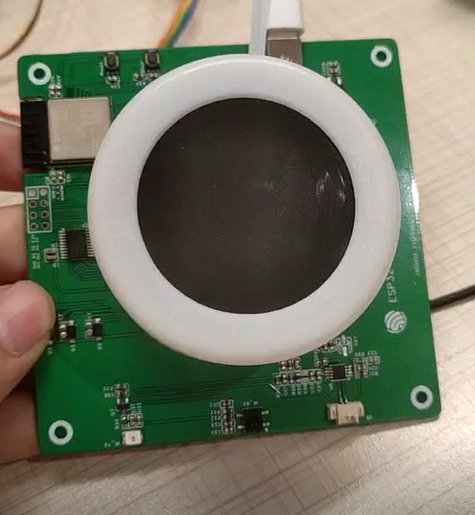
Sensorless square wave ADC solution: Supports pulse method rotor initial phase detection, ADC sampling zero-crossing detection, stall protection, etc. Suitable for small household appliances and industrial automation applications.

The summary is as follows:
Solution Category |
Solution Name |
Master Control |
Motor |
Function |
Component |
Application Scenario |
---|---|---|---|---|---|---|
Floor Fan Solution |
ESP32-S3 |
Brushless DC Motor |
Supports RainMaker remote control, speed adjustment, oscillating control, natural wind speed, and other functions |
Smart home appliances and industrial automation scenarios |
||
FOC Single Motor Drive Solution |
ESP32-C3 |
Brushless DC Motor |
Supports speed closed-loop, angle closed-loop, and torque closed-loop |
Smart home appliances and industrial automation scenarios |
||
FOC Knob Screen Solution |
FOC Smart Knob Screen |
ESP32-S3 |
Brushless DC Motor |
Supports boundary-free/boundary-based ratchet knob tactile simulation |
Knob screen application scenarios in small home appliances |
BLDC Reference Materials
In addition, we currently have some public brushless motor (BLDC) github software libraries, videos, and module materials, as follows:
Software References
Module/Development Board Materials and Option References
BLDC Drive Solution Summary
In the brushless motor (BLDC) solution, driving the three-phase inverter circuit is an important link. In ESP chips, the LEDC and MCPWM modules are supported for driving the three-phase inverter circuit.
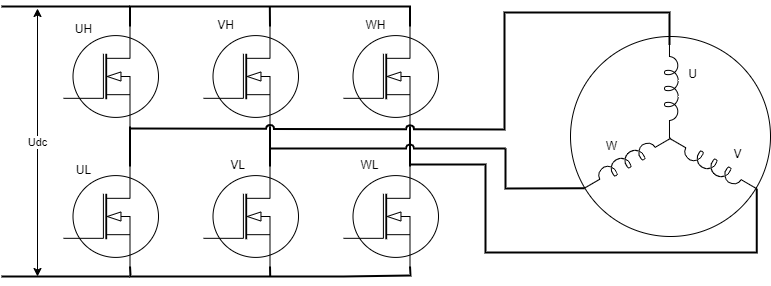
MCPWM Drive Solution
MCPWM is a multifunctional PWM module that supports multi-channel PWM output, external pulse width calculation, etc. Some ESP chips do not support MCPWM, such as ESP32-S2, ESP32-C3, etc. In the MCPWM drive scheme, the control of the BLDC motor is realized by configuring the phase, duty cycle, frequency, etc. of the MCPWM module.
Note
Does it support outputting complementary waveforms to control MOS drivers?
Yes, the MCPWM generator module supports generating independent or complementary PWM waveforms, which can control MOS drivers by configuring output pins.
LEDC Drive Scheme
LEDC is mainly used to control LEDs, but it can also generate PWM signals for driving BLDC motors. All ESP chips support PWM output driven by hardware LEDC.
Note
What are the scenarios for using LEDC drive? Is the sensorless BLDC square wave control scheme supported?
The ESP_SIMPLEFOC component supports configuring LEDC channels to output PWM signals for driving BLDC motors. In the scenario of sensorless square wave control scheme, considering the accuracy of the sampling moment, it is recommended to use the MCPWM drive scheme.
Summary of Common BLDC Questions
Q: How to control the demand for Espressif chip selection?
A: Currently, Espressif mainly promotes the BLDC control scheme based on ESP32-S3, which supports sensorless BLDC control schemes based on ADC or comparator and sensor FOC control schemes. In addition, users also need to consider the detailed parameters required by the application, such as the number of IOs, memory and flash size, etc. You can refer to Espressif’s official selection tool or consult business.
Q: Which version of ESP-IDF should be used for the development of BLDC control schemes?
A: ESP-IDF 5.0 and above versions need to be ensured.
Q: Can you assist in the development of BLDC brushless motors?
A: Yes. First, users need to determine the motor model according to application requirements, including whether it is a brushless DC motor, motor parameters, etc. At the same time, users need to clarify control requirements, including speed control, angle control, torque control, etc. Then, according to the motor type and control requirements, assist users in brushless motor development.
Q: What is a BLDC driver? How do ESP series chips cooperate with it?
A: The drive circuit of the brushless motor (BLDC) mainly uses a three-phase inverter circuit to generate magnetic fields in different directions to drive the motor. Among them, the ESP chip mainly controls the gate drive chip to control the BLDC brushless motor by generating PWM signals through the MCPWM or LEDC module.
Q: Why is the MCPWM drive scheme recommended in the BLDC scheme?
A: MCPWM is a dedicated peripheral in ESP chips for motor and power control. Each MCPWM peripheral includes a clock divider, three PWM timers, three PWM operators, and a capture module. By configuring the MCPWM module, accurate sampling of the BLDC brushless motor can be achieved.
Q: What is the difference between the sensorless square wave BLDC component and the ESP_SIMPLEFOC component?
Answer: The Sensorless Square Wave BLDC Component is mainly used for implementing sensorless BLDC motor control, supporting external comparators and ADC to monitor back EMF for sensorless speed closed-loop control. The ESP_SIMPLEFOC Component is a sensor-based FOC control solution based on the SimpleFOC algorithm, supporting IDF framework development, and meeting the needs of different user groups. If there are no external sensors, it is recommended to use the Sensorless Square Wave BLDC Component.